

#FLYCUT OR END MILL TO REMOVE MATERIAL SERIES#
My point is a series 1 bridgeport like all machines has its limits and its usually roughly 1hp and even using 3/4hp at the tool you can get serve vibration chatter tool damage and possible machine damage at collet set screw key especially at low rpm. so its a choice stall motor if cutting too much or have collet spin damaging taper on overload. The set screw key for R8 collet keeps it from spinning and damaging taper. you can say those parts acts as a fuse but the fuse is not so easy to replace if damaged just saying you got any machine especially low hp machines got to think what damage will occur if you overdue it. once damaged repairs are not so easy without major disassembly. obviously if using a 1.5" dia tap and using a 18" wrench to turn tap the little lock pin maybe 0.2" in dia engaged in a soft aluminum or zinc alloy gear aint going to hold the back against the tapping force. This is very similar to using a big tap on a small lathe with the headstock lock pin engaged to hold chuck from turning. Obviously if i knew it would get damaged so easily i wouldnt have pushed the mill so hard when damaged none of collets want to go in quite right cause set screw key squashed bent a bit set screw replacement is a relatively annoying thing to have to do.
#FLYCUT OR END MILL TO REMOVE MATERIAL MANUAL#
Set screw key replacement usually you need the maintenance manual as repairing the head often requires certain steps to do repairs successfully. when on low gear you have a relatively large amount of cutting forces but the wack wack wack is hard on the mill boss gives you a job and wants it done as fast as possible.
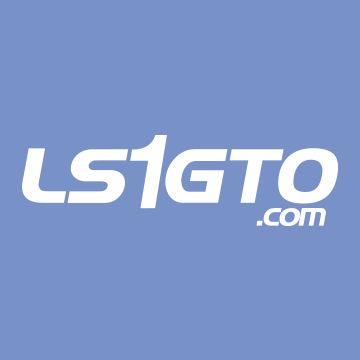
I have damaged key and key way on bridgeports before flycutting up to stall point. Carbide isn't always the best choice for cutting metal but it is more expensive. You can always spend more money later on more expensive tooling if you need/want to. Use cutting oil, set your spindle speeds per diameter and material (use guards when cutting) and find what works for you. Do make sure the set screws are locking the bit in for safety. If you're new at this I suggest a "lathe tool" type of single bit using a HSS bit to get familiar for the lowest cost. The multi insert type isn't as susceptible to shock like the single bit are but still have comparatively short life for the inserts, particularly in a mill like a Bridgeport. This is useful for harder materials, stainless steel, or have a large plate to deck down to thickness. The other type some call a fly cutter is a multi insert tool that does use carbide inserts. Hot chips are thrown everywhere so guards are important or you'll catch a hot chip down your shirt or have a large area around the machine to sweep up. Fly cutting demands you tram the mill head fairly close or you'll be cutting an angled and/or concave surface. While spindle speeds are much slower I prefer using HSS for use in a fly cutter as it resists shock much better and touching up the cutting edge is much less work. You can use carbide but I've never been a fan of this due to the shock of an interrupted cut which chips the brittle cutting edge. Thus, high speed diamond machining offers several advantages, let alone a major reduction of machining time.If I understand your question correctly using the term "lathe tool holder" than that suggests carbide inserts and a single cutting edge. High speed diamond machining may also yield an improved surface roughness which was confirmed by comparing the step heights at grain boundaries obtained in diamond milling of OFHC copper and brass CuZn39Pb3 at low (v c = 100 m/min) and high cutting speed (v c = 2000 m/min). Furthermore, it was found that the rate of chemically induced tool wear in diamond milling of steel is decreasing with decreasing tool engagement time per revolution. Fly-cutting experiments carried out at low (v c = 380 m/min) and at high cutting speed (v c = 3800 m/min) showed that the rate of abrasive wear of the cutting edge is significantly higher at ordinary cutting speed than at high cutting speed in contrast to the experience made in conventional machining. In face turning experiments with constant material removal rate the cutting forces were recorded as a function of cutting speed between v c = 150 m/min and 4500 m/min revealing a transition to adiabatic shearing which is supported by FEM simulations of the cutting process. We have investigated the cutting forces, the tool wear and the surface finish obtained in high speed diamond turning and milling of OFHC copper, brass CuZn39Pb3, aluminum AlMg5, and electroless nickel.
